项目通过引入智能制造技术和数字化生产工具,实现生产过程的数字化、自动化和智能化。通过对工艺流程的优化和智能化改造,能进一步实现生产线的高效运行和灵活生产。采用MES和WMS等管理工具,能深入分析生产流程和设备状态,识别并消除浪费,从而优化生产线的布局和作业流程,提高资源利用率和生产效率。充分建立数字孪生模型、实时监控和远程控制系统,能够实现对生产线的全面监控和实时调整,从而提高生产响应速度和产品质量一致性。借助数据分析技术,定期检查设备的机械零件、电气元件和控制系统,及时更换磨损件,这有助于延长设备的使用寿命和保证生产线的稳定运行,实现生产过程的智能优化和预测性维护。利用大数据分析和机器学习算法,有效挖掘生产数据的潜在价值,充分预测设备故障和生产异常,并且提前采取措施,能避免生产中断和品质问题,从而提高生产线的稳定性和可靠性。
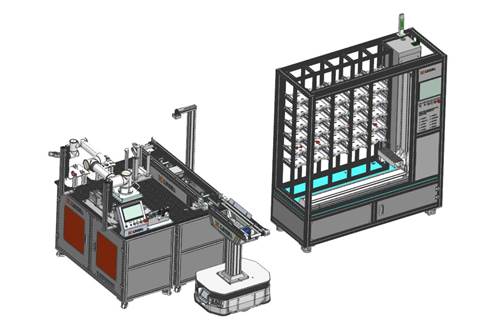
项目平台主要能够实现以下功能:
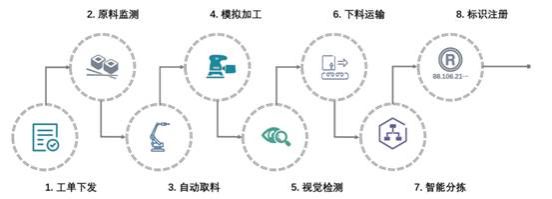
本项目主要完成汽车心轴的全过程自动化检测与装配并通过数字孪生及数据库管理,进行精益化管理与预测性维护。根据装配步骤及配套模块和软件对工艺流程进行分析,如图所示。
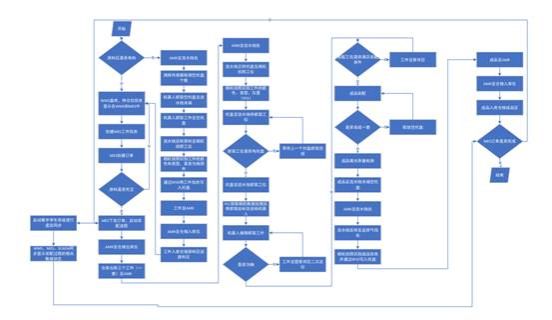
工艺流程图
主体装配流程描述如下:
1. 首先进行原料自动检测入库,协作机器人将原料抓取至智能视觉工位进行检测,识别出是否为残损件,并对识别出的工件进行RFID标记,由AMR机器人转运至智能仓储模块存储至指定仓位(残损件仓位或原料仓位);
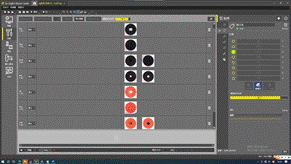
2. 通过WMS仓储管理系统进行原料盘点,获取详细的原料信息(数量、类型、颜色、仓位),完成对原料的整理和筛选并同步至MES系统中;
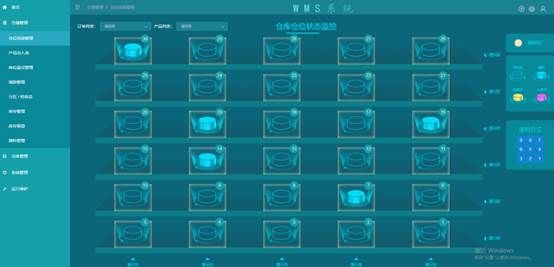
3. 在MES系统中创建产品信息列表,并从列表中选取对应工件创建订单并下发给立体仓库,仓库WMS系统完成原料出库,由AMR机器人将原料转运至智能装配检测模块;
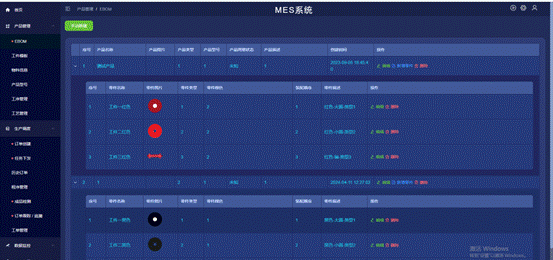
4. 智能装配检测模块输送线将工件输送至智能相机工位进行拍照识别,获取工件的信息(颜色、类型、及抓取坐标),通过PLC计算处理后发送给协作机器人将识别出的工件抓取并放置到对应的暂存区等待装配,同时机器人将空托盘放置托盘存放区;
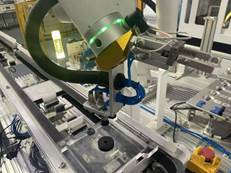
5. 订单对应的工件数量匹配后启动装配流程(装配完成有激光传感器检测是否装配到位),协作机器人将成品放置在成品暂存区,并将对应信息同步至MES系统;
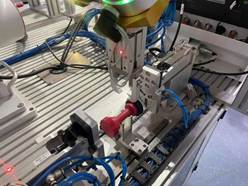
6. MES系统判断订单完成后,启动成品入库流程,成品由协作机器人放置到输送线拍照工位由智能相机拍照判断是否合格,同时将合格的成品信息通过RIFD录入托盘对应芯片中;
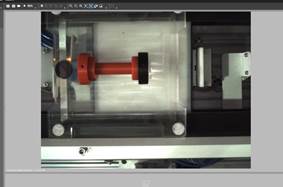
7. AMR机器人运行至装配模块等待接受成品,并将成品运送至立体仓库入库位,码垛机器人根据WMS系统中的入库指令,将成品放置到对应库位中并同步信息至MWS系统中,同时AMR运行至等待位置结束整个装配流程;
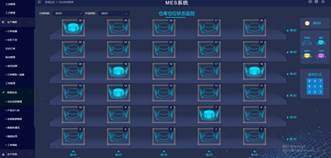
8. 全过程启动数字孪生系统实时通过仓储及装配过程,实现紧密的数字化可视化;
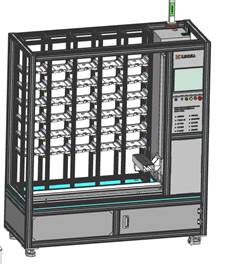
9. 通过数据信息采集,生产过程的传感器、物料、电压电流、气压、AMR电池状态、机器人关节信息等数据都能实时显示到SCADA系统终端上,实现数据的同步和可视化,并通过MES系统对数据分析,提供订单分析、电量分析等提高生产效率的精益化管理。
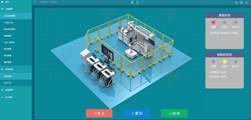
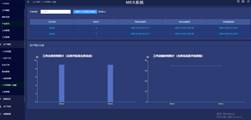
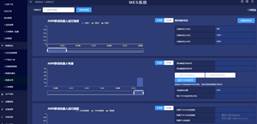
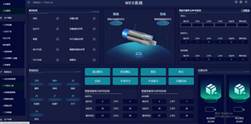